Numerous Fraunhofer-Institutes, universities and industrial partners participate in SynErgie. But what is the role of Fraunhofer IWU?
During the first phase of the project (2016-2019), Fraunhofer IWU including colleagues of the Zukunftsfabrik team, carried out different activities to lay the foundations for energy flexibility in factories in the field of forming and machining. Firstly, an awareness campaign on energy flexibility was launched in the form of workshops for industrial partners. Thus, they were brought to the attention of the benefits, challenges and necessary steps to become an energy-flexible factory.
Secondly, an estimation of the flexibility potential in the participating production plants was produced. After a measurement campaign on the relevant consumers at the level of component, machine, plant, and distribution, an exhaustive database for forming, press hardening, machining and assembly processes was created. In order to prioritize flexibility measures at different levels, an evaluation system was generated that allows comparison and facilitates decision-making and the selection of different options by the company.
Stemming from the collected data, concepts were developed to allow machines, systems, and processes to work flexibly. Said concepts cover machine design, IT tools and organizational solutions that influence load behavior. Among them an innovative bivalent burner concept for press hardening was devise that can work with natural gas as well as with electricity.
In relation to the development of planification strategies and production control, an analysis on the effect of changes over product quality was carried out. Besides, the impact of plant stops, and process interruptions was studied. Most use-cases would be feasible in the event of short pauses up to fifteen minutes. For longer interruptions, simulation models were produced in order to determine the energy needs and logistics of each production phase, and thus be able to efficiently plan stoppages and changes in production pace.
The results of the first phase were particularly favorable in the field of hot forging; including other processes, the energy flexibility potential of a single factory can reach up to several megawatts. Moreover, the work of Fraunhofer IWU highlighted the impact of energy flexibility over production infrastructure, and that it is not only technological solutions that have a key role to play in achieving this goal. Therefore, the challenge to overcome is the effective connection of the different systems involved in the production process, so that flexible loads can be efficiently managed and controlled.
What about the second phase?
Large part of the work during the second phase was precisely focused on this last issue. To begin with, it involved the creation of an energy-oriented production planning and controlling service, or ePPS (energieorientierte Produktionsplanung und -steuerung) for its acronym in German. This service was developed taking a factory from Hirschvogel Group as reference but with the idea of making it transposable to other production plants. It consists of three components, the first one of which enables the company to preselect different energy flexibility measures on the company’s platform. Next, the second component simulates the production process and provides extensive information on both energy and material flows. Finally, the last subservice allows for the optimization of the process according to the energy flexibility measures (e.g., postponing the production order start). The performance of each optimization is then reevaluated and the results are made available on the company’s platform.
As an additional service to ePPS, a feature for intelligent load-management was developed. This system uses dynamic load specifications as well as forecasts from production, energy infrastructure and energy market in order to control machinery and equipment. The planning element of this service, together with ePPS, allows to manage production processes and loads, and schedule the use of energy infrastructure such as batteries or CHP units according to target criteria. The produced data is used by a dispatch module that connects or disconnects machines and systems and increases or decreases the pace of production according to energy consumption data, machine priorities, production availabilities or production orders.
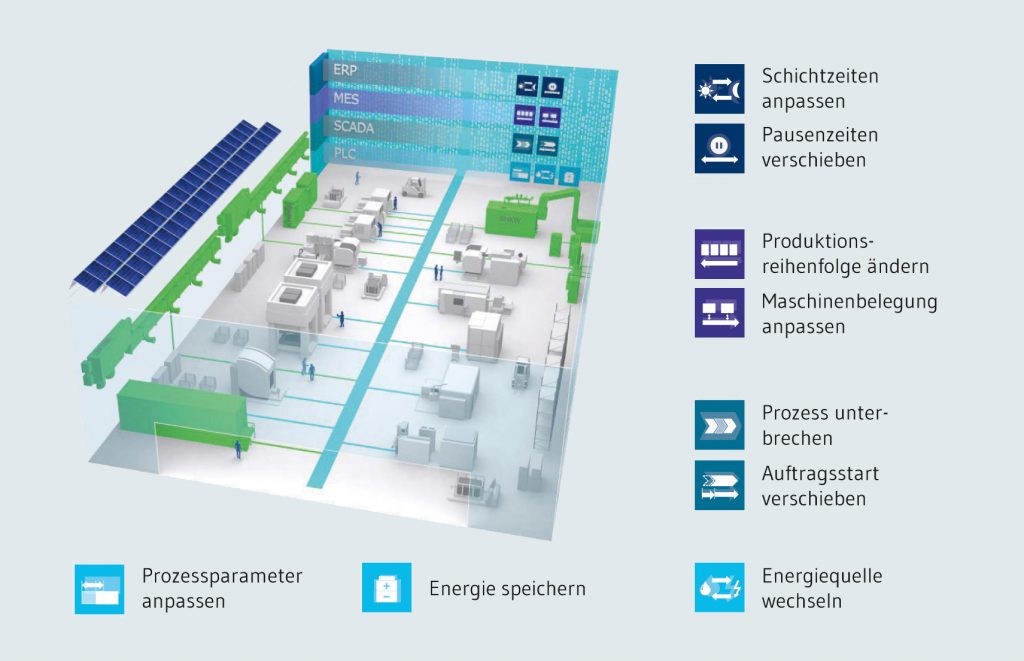
Figure 1. Energy-flexible factory operation (based on Graßl, 2015). © Fraunhofer IWU
Furthermore, Fraunhofer IWU contributed to the activities of several partners in other work packages. For example, by studying the influence of flexibility measures on voltage quality and reactive power at the electricity supply network, or by evaluating different flexibility solutions regarding their CO2 footprint. Further endeavors in the areas of bivalent heating and sector coupling in the forging industry are described in this article.
What’s going to happen in the third phase?
The third and last phase will begin this year 2023 and will mainly consist of testing all the measures, functionalities and services that have been developed so far. Thus, Fraunhofer IWU will keep on collaborating with its partners on industrial demonstrators to collect data on energy-flexible production processes, which will ultimately serve to its optimization. Work will continue on long-term load and energy management, to find a tailor-made flexibility strategy for each industrial partner to exploit its full potential.
Finally, the energy-synchronization platform will be further improved, so much the different company platforms as much as the one for interconnection and market access. In the end, the goal is to build a secure, solid system that efficiently integrates all the innovations generated during the project and to gain the necessary knowledge to extend this model inside Germany.
Sources:
Graßl, M. (2015). Bewertung der Energieflexibilität in der Produktion. Retrieved January 26, 2023, from https://www.utzverlag.de/assets/pdf/44476dbl.pdf
IRENA (2018). Power system flexibility for the energy transition, Part 1: Overview for policy makers. Retrieved January 25, 2023, from https://www.irena.org/publications/2018/Nov/Power-system-flexibility-for-the-energy-transition
Sauer, A.; Abele, E. & Buhl, H. U. (2019). Energieflexibilität in der deutschen Industrie. Retrieved January 25, 2023, from https://synergie-projekt.de/wp-content/uploads/2020/08/urn_nbn_de_0011-n-5659211.pdf
Sauer, A.; Buhl, H. U.; Mitsos, A. & Weigold, M. (2022). Energieflexibilität in der deutschen Industrie. Band 2: Markt- und Stromsystem, Managementsysteme und Technologien energieflexibler Fabriken. Retrieved January 25, 2023, from https://synergie-projekt.de/wp-content/uploads/2020/08/SynErgie_Band_2.pdf
Statista (2022). Verteilung des Stromverbrauchs in Deutschland nach Verbrauchergruppen im Jahr 2021. Retrieved January 25, 2023, from https://de.statista.com/statistik/daten/studie/236757/umfrage/stromverbrauch-nach-sektoren-in-deutschland/
Universität Stuttgart (n. d.). SynErgie. Retrieved January 25, 2023, from https://synergie-projekt.de/
Kommentare hinzufügen